武田機(jī)電
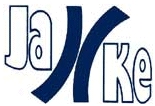
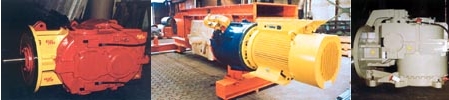
JAKE減速機(jī),JAKE齒輪,JAKE齒輪箱
JAKE齒輪箱廣泛應(yīng)用于風(fēng)能,礦山等重型工業(yè)領(lǐng)域.
Wind Power Special gears for wind power systems Our performance range is extensive, featuring an abundance of unique benefits for you. We draft, design and engineer gears for rotor outputs of 150 to 2,000 kW and upwards. The major emphasis of our work is meeting your individual needs. We start off in the consultation phase by jointly outlining strategies for your special application. You have a totally committed and highly qualified team of experts at your disposal. This thorough consultation work saves you time and prevents making the wrong decisions. After we have outlined the design proposal according to the information you provide, then we translate it into reality. That spells out on-time production on state-of-the-art equipment with highly stringent quality monitoring. We can streamline gear engineering and even come up with new ideas by perfecting specific gear components such as the gearing, bearings, seals, lubrication monitoring, temperatures and oscillation-resistant design.
Mining For such things as chain conveyors and plough systems JaKe has a range of the best gear designs, our building block system, in stock for any and all drive designs you need. From the spur gear and straight bevel gear pair right down to planetary gears, JaKe's high-performance mining gears are used all over the world to the satisfaction of customers at drive outputs upwards of 1,000 kW. We have a wide range of gear reduction gradations for all gear models for precisely matching gear reduction. JaKe's gears are excellently suited for attaching constant- and multiple-speed electrical motors in connection with torsionally elastic or turbo-clutches. Technical Features Drag link conveyors up to 1,000 kW as cone planetary or planetary gears, conveyor belt gears or as straight bevel gear, spur gear or planetary cone gears
Cement, stone and earth industry JaKe's gears for the cement, stone and earth industry are used for breaking, crushing, grinding, compacting and briquetting including transportation. That means that JaKe features the established reliability strategy for meeting these drive challenges under particularly difficult conditions such as performance class upwards of 5,000 kW for crushing drives. Technical Features Gear designs as spur gears, straight bevel gears or planetary gears depending upon the installation situation and with or without differentials in horizontal or vertical designs Distortion-resistant and low-oscillation gearbox cases Preventing overload breakage of gearings and guaranteed operational reliability with gear tooth base-reinforced K gearings at very large modules HPG-geared or gound bevel wheels Optimum low-wear sealing for very dusty working conditions Optimum regulation for thermal economy Officially accepted by official inspection agencies (certificates as per EN 10204) Up to three times the starting momentum that can be transferred towards the rated output
Conveyor Equipment Thanks to its enormous range of performance and its sophisticated quality, JaKe's special gears have been effectively used in conveyor equipment for years. JaKe's gears are engineered for a variety of machines and systems such as bucket wheel excavators, reclaimers, overburden spreaders, conveyor belts, hoisting gears, clamping winches, swing gears, crushers and spillage belts. When designing gears for bucket wheels, JaKe realises that torques have to be transmitted with great reliability. These gears also have to be built in weight-saving designs to place a minimum burden on the boom design. JaKe's gears for conveyor systems We not only place a premium on no-wear, oil-tight shaft seals with belt gears. Our gears are tight – put us to the test! All of the well-known mining operations use our gears
Shipbuilding We apply the knowledge from dredging to developing new propeller gears to offer our customers a high degree of reliability even under extreme conditions. JaKe’s internal standards in calculating and designing propeller gears guarantees a high level of additional reliability that meet and surpass the classification regulations. We not only work in series production, but also build customised equipment. Technical Features: propeller gears ranging from 3,000 kW to 30,000 kW single-in / single-out twin-in / single out with and without multiplate clutches secondary or primary PTO PTI / PTH generator gears from 500 kW to 15,000 kW front-end design hollow-shaft gears Customised work is also one of our strengths
Rubber/Plastic We design robust and long-lived gears for the special needs of the rubber and plastic processing industry – always tailor-made to special applications in calendars, extruders and mixers. Our range of products includes: 1-shaft extruder gears with a hollow-shaft drive 2-shaft extruders mixers gears calendar and kneader gears Technical Features reduced-noise design above-average service life built-in axial bearing for supporting the worm back pressure forces separate bearings for absorbing tensile forces patented hydrostatic bearings for 2-shaft extruders 2-shaft extruder gears with optimum power transfer at low shaft space 2-shaft extruder gears with the same or opposite direction of shaft rotation
Rolling Mill Technology Rolling mills depend on robust, low-noise gears with high reliability and a long service life. Not only gearings and bearings, but also gearbox cases designed for rolling mills have to absorb great impact and axial forces from joint spindles. Our special programme focuses on warm and cold rolling mill gears such as comb rolling gears, reel gears and reciprocating rolling mills and high-speed wire blocks and aluminium foil rolling mills. Technical Features double spiral geared pinion rollers forged from one piece frequent use of K-gearing together with large modules rolling bearings with a calculated service life in excess of 50,000 operating hours also designs with friction bearings test certificate as per EN 10204 high gearing qualities (to 5) – especially important with high circumferential speeds and noise reductions pinion roller and reel switching gears with built-in centrifugal force guard for various rolling speeds special seals for drive shafts and driven shafts
Sugar Industry The harder the competition, the more important it is to have a competitive edge with enhanced product quality and higher production quality. That's reason why high-quality technological gears are crucial to the sugar industry because the campaign has to be seen through without expensive downtimes. State-of-the-art gear engineering now lets you tap essential reserves of productivity. JaKe has all the expertise you need in developing special gears because JaKe's special gears have been used in the sugar industry for more than 40 years. With their reliability and long life, they meet the important challenges of constantly increasing demands in sugar beet processing in a wide variety of machines such as shaving presses, mashing, washing, conveyor systems and agitators, etc. Longstanding business relationships with companies operating on an international scale such as Krupp, Buckau-Wolf, BMA, Selwig & Lange, Salzgitter-Weigel-Werke, Babbini and Stord-International and maintaining contact with the operators of these systems gives us the experience we need for streamlining and boosting the performance of your plants. New Developments JaKe has once again proven its technological expertise in gear engineering with prominent new developments for 2-shaft shaving presses. These press gears have been in use for many campaigns without even the slightest hint of failure. Technical Features Gears new developments for 2-shaft vertical and horizontal design shaving presses verified torque division and thrust bearing design various different types of arrangements with V-belts or direct drive drive motor position as per the customer’s choice mechanical speed changes with built-in switching systems, such as 0.75 min-1 for high dry substance, or 5 min-1 for major clipping throughput at least twice the reliability in relation to rated output and in the entire speed range lower costs from speed change means no expensive electrical variable speed motors due to the correct design of the mechanical switching system the design of the preliminary gear can be changed while maintaining the design of the main gear Streamlining and Modernising boosting torque by as much as 50% with constant building volume on existing gears boosting service life on existing gears streamlining lubrication on existing gears no change in foundations if JaKe retrofits since the gear connecting dimensions are adapted trained personnel install gears
Special Gearing The quality demanded of JaKe's special gearing: all gearing is hardened and ground in application we raise tooth-break reliability by approximately 10%-15% with transverse tooth base polishing (known as the ZQP process) on tooth stages subject to special stress we achieve optimum load transfer ability by intelligently co-ordinating contact angles, tooth base radiuses, protuberances, teeth depths, load flank grinds for gearing and a finite-element calculation for cases (as requested)
Dredging Imagine how much experience we have in dredging! There's more than 25 years between our first cutter head gear and the largest in the world. One-quarter century of experience from tough real-life practice we get from dredging waterways and docks. We manufacture gears for drives of 150 kW to 30,000 kW. Real-life practice sets the requirements made of marine gears. Major reliability is one of our foremost criteria. Our gears for cutting head and pinion-type cutters, winches, sand pump generators and propeller shaft drives are in use under the toughest conditions on all the world's oceans. They have proved that they are extremely reliable and efficient under the most difficult weather conditions. If you've got the right drive, you build better products. And, no matter how you look at it, we've got the better drive. Wide range of applications There is a wide range of applications for marine gears and the demands are great because they have to work under tough and often very unfavourable conditions. But, when the going gets tough, that’s when our gears get going. Be it a cutter head gear or pinion-type cutter for dredging waterways and docks, as gears for excavator pumps used underwater, on deck or in the engine room, as a winch gear for spooling off cables or as propeller shaft gears – our gears are engineered with state-of-the-art construction that have proved their worth in real-life situations.